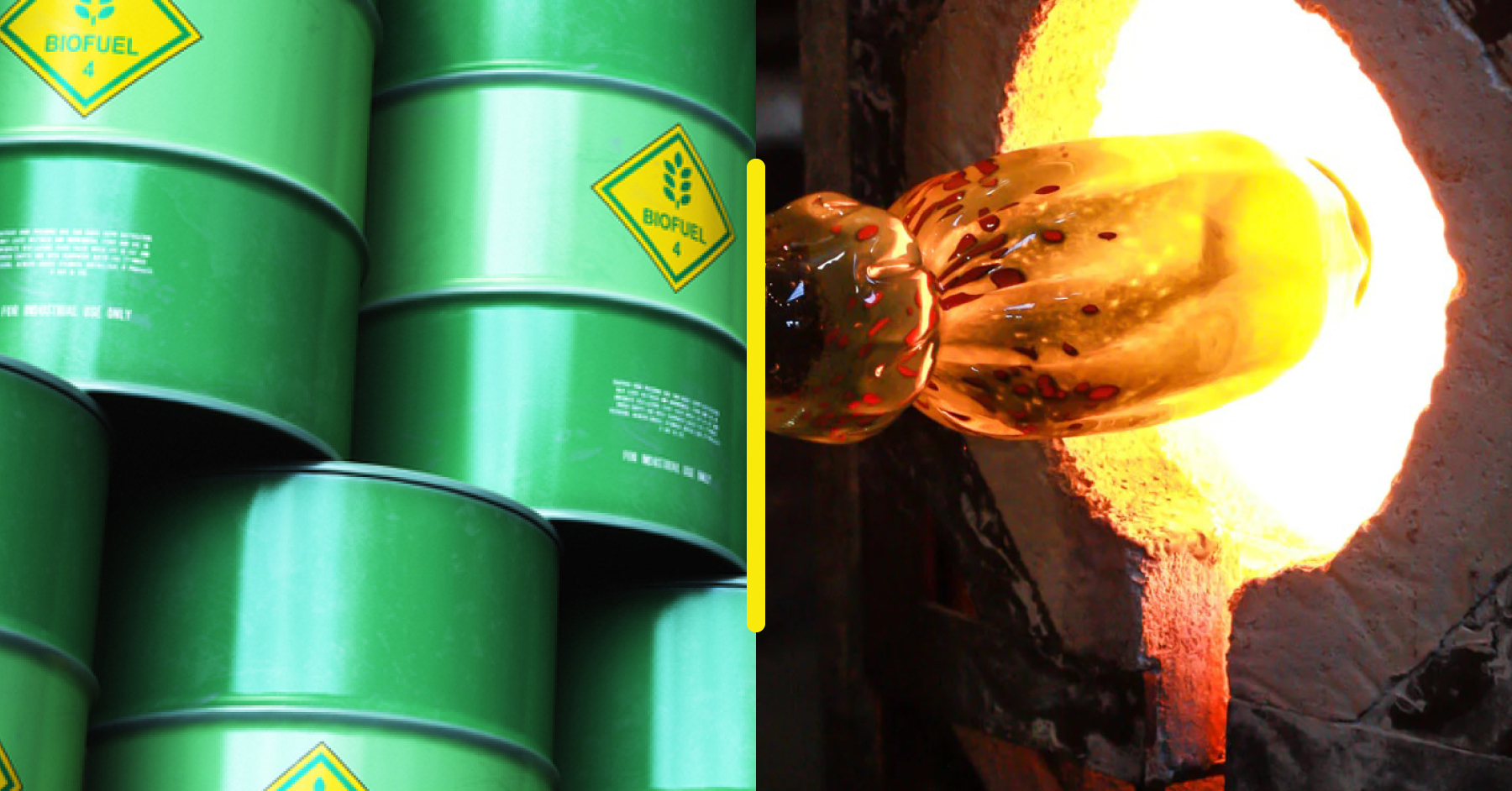
Delve into the innovative world of sustainable energy solutions, from biofuels and hydrogen and waste-to-energy technologies. Learn how these cutting-edge alternatives are revolutionizing glass manufacturing processes, reducing carbon emissions, and paving the way for a more efficient future.
Biofuels exhibit a distinct quality, burning with a radiant flame and containing higher moisture content than conventional natural gas or hydrogen fuels.
The mesmerizing nature of glass never fails to captivate everyone. Its brilliant radiance transports all to a different realm, causing us to lose track of time. Particularly during the nighttime, when we gaze upon towering skyscrapers or hear the distinctive clinking of glassware on our dining table, its allure is irresistible. The applications of glass are boundless. Its origins can be traced back thousands of years, preceding the discovery of iron smelting. In ancient times, Stone Age societies utilized naturally occurring obsidian glass for its ability to fracture into razor-sharp edges, making it invaluable for tools and weapons.
The glass industry has since undergone significant evolution, ushering in a plethora of diverse forms and applications across various sectors. However, there is a drawback we must address. Despite its immense utility, the production of glass emits large quantities of CO2, thereby exacerbating environmental concerns. In this blog, we will delve deeper into the glass sector and explore alternative methods to mitigate its emissions.
An Overview on Glass Manufacturing
Glass, a non-crystalline solid, possesses remarkable qualities including transparency, brittleness, and chemical inertness. Its practical and decorative uses are widespread, ranging from window panes to tableware and optics.
Glass is made through a process that involves melting sand and other ingredients, and then cooling the molten material to form a solid. The main components of glass include silica (silicon dioxide or quartz), soda, and limestone. Silica is the primary constituent of sand, accounting for its abundance in glass production.
The production of glass typically starts with the collection of silica-rich sand, which is then heated to high temperatures in a furnace. The heat causes the sand to melt and transform into a liquid state. Other ingredients such as soda and limestone are
added to the molten sand to modify the properties of the glass. These additional ingredients help to lower the melting point of the mixture and improve its workability.
Once all the ingredients are thoroughly mixed, the molten glass is then formed into the desired shape through various methods such as pouring, blowing, or pressing. Depending on the specific application and desired properties, additional processes such as annealing (controlled cooling) and tempering (strengthening) may be applied to enhance the glass’s durability and strength.
It is important to note that there are different types of glass with varying compositions and production methods based on their intended use. For example, soda-lime glass, which contains about 70% silica, is the most commonly used type of glass and is used in applications such as window panes and bottles.
In summary, the process of making glass involves melting sand and other ingredients, shaping the molten material, and then cooling it to form the final solid product. The specific composition and production methods may vary depending on the type of glass being manufactured.
How CO2 Emissions Happen in the Glass Industry?
In the glass manufacturing industry, CO2 emissions from furnaces primarily occur due to the combustion of fossil fuels used for heating and melting the glass batch. Furnaces are essential for maintaining the high temperatures required to melt the raw materials and transform them into molten glass.
Here are a few key points regarding CO2 emissions in glass manufacturing via furnaces:
- Combustion of Fossil Fuels: Furnaces commonly use natural gas, coal, furnace oil as fuel sources for the combustion process. These fuels release carbon dioxide (CO2) when burned, contributing to greenhouse gas emissions. The amount of CO2 emitted depends on factors such as the type and efficiency of the furnace and the fuel used.
- Energy Consumption: Glass furnaces require substantial amounts of energy to achieve the high temperatures necessary for melting the glass batch. The energy for heating the furnace is often derived from the combustion of fossil fuels, which leads to the associated CO2 emissions.
It’s worth noting that the choice of fuel can depend on various factors, including the availability and cost of the fuel, environmental regulations, energy efficiency considerations, and the specific requirements of the glass manufacturing process. Some glass manufacturing facilities also invest in energy-efficient technologies and alternative fuels, such as biofuels, to reduce their environmental impact and operating costs.
Alternative Fuel Technologies
Biofuels, sourced from organic materials, mark a sustainable energy alternative. When integrated with carbon capture techniques, they pave the way for glass manufacturing to achieve net-negative CO2 emissions. Biofuels exhibit a distinct quality, burning with a radiant flame and containing higher moisture content than conventional natural gas or hydrogen fuels. This unique composition enhances heat transfer to the glass melt. Additionally, due to their lower flame temperature, biofuels are expected to emit reduced levels of NOx, further contributing to a greener, more eco-friendly glass production process.
Another alternative fuel switching technology being explored in the glass sector is the use of hydrogen fuel. Hydrogen is known for its clean combustion properties, as it produces only water vapor when burned. Glass manufacturing research programs, such as the Glass Futures’ Industrial Fuel Switching Phase 3, are investigating the feasibility and benefits of utilizing hydrogen as a fuel source for glass furnaces.
Hydrogen fuel has the potential to significantly reduce carbon emissions and provide a greener energy source for glass manufacturing. However, challenges such as infrastructure development, cost-effectiveness, and ensuring a consistent energy supply need to be addressed before widespread adoption of hydrogen fuel in the glass industry can be realized. Nevertheless, the research and development efforts in this area are crucial steps towards decarbonizing the glass manufacturing process.
Challenges and Solutions
While alternative fuel switching technologies hold immense promise, challenges such as initial capital investments, infrastructure upgrades, and energy storage limitations need to be addressed. Governments, industries, and research institutions are collaborating to find solutions, offering incentives, subsidies, and research grants to accelerate the adoption of these technologies. Read this blog also: Bio Furnace Oil for Foundries: A Time and Money Saving Solution for Foundries
Final Thoughts
The glass industry stands at a pivotal moment in its history, propelled by a collective commitment to sustainability and innovation. Alternative fuel switching technologies are not just a pathway to reducing carbon emissions; they represent a fundamental shift toward a greener, more sustainable future. As research and development continue to drive advancements in biofuels, hydrogen production, waste-to-energy processes, and electrification, the glass sector is poised to become a beacon of environmental responsibility and technological progress.
Elevate your industrial operations with Buyofuel, India’s premier online marketplace connecting you directly to top-tier Bio Furnace Oil Manufacturers & Suppliers in India. At Buyofuel, we redefine energy sourcing, offering a seamless platform where quality meets convenience. Don’t miss out on the opportunity to make a difference in your industry.